Extruding
The extruding process and insulates wire and cable and protects them in abrasive environments. Your wire or cable will last longer, and you will save time and money with future replacements.
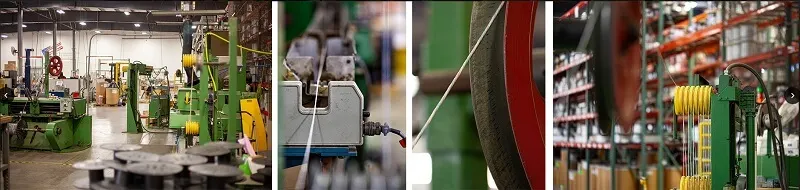
Extruding
The extruding process is when a wire is pulled through a heater polymer. The polymer resin coats the exterior of the wire and is then cooled, solidified, and inspected. This gives the wire an extra layer of protection.
The Science
Before extrusion, a polymer is often blended with additives and other materials. Once the polymer or blend is properly dried and ingredients are mixed, the formulation is fed into the extruder. In the extruder, the polymer or blend is melted, mixed, and delivered to the die to shape the extrudate.
After exiting the die, the product is cooled, solidified as a coating in the desired shape, and pulled away from the extruder at a constant velocity to attain the thickness and coating required. The product is then shock tested and inspected for quality, insulation, and usage.
Allied Wire and Cable provides two types of insulation:
FEP - Fluorinated Ethylene Propylene
ETFE - Ethylene Tetrafluoroethylene
Curious About Other Services?
Download our Informative PDF that breaks down a few of Allied Wire & Cable's Value-Added Services.